На месторождении-ветеране «Газпром добыча Надым» продолжается внутритрубная диагностика газопроводов. Специалисты исследуют межпромысловый коллектор, откуда добытые и очищенные углеводороды отправляются в газотранспортную систему России. На это время нитку вывели из строя, сложная и многоступенчатая процедура проходит в несколько этапов. Приступив к работам в мае, сегодня газовики близки к завершению масштабного комплекса испытаний.
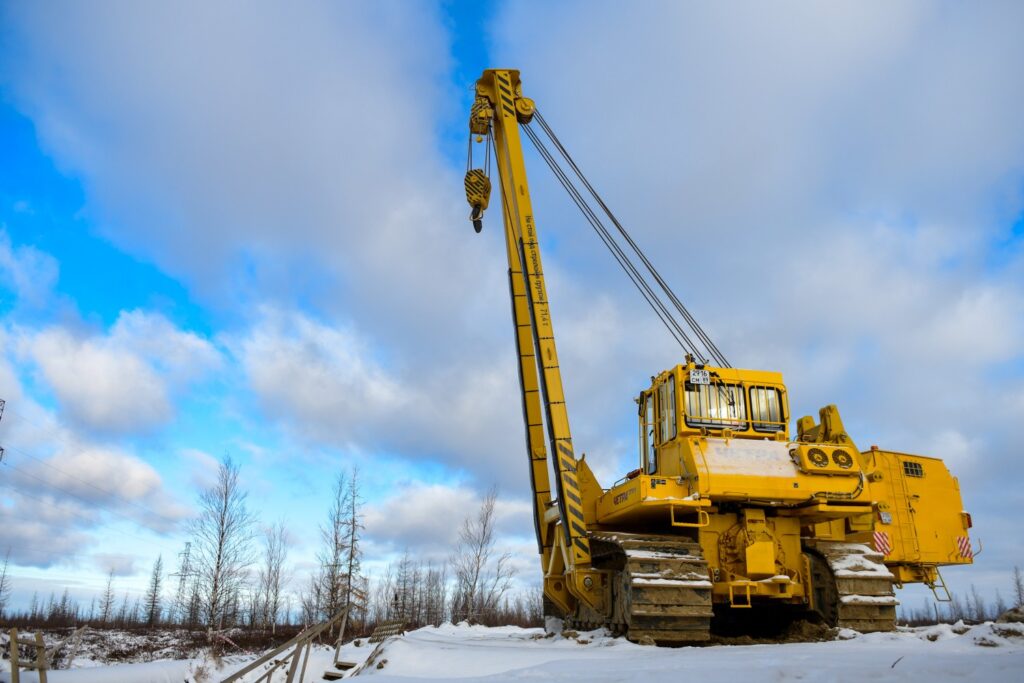
Внутритрубная диагностика предназначена для определения технического состояния газопровода с использованием специальных поршней, магнитных дефектоскопов. Вместе с потоком газа они проходят по линии и регистрируют возможные погрешности, которые могли возникнуть за годы непрерывной эксплуатации. На сегодняшний день это самый информативный метод в отрасли, он позволяет получать точные данные о состоянии так называемых ниток, оценить в деталях особенности сварных соединений, отследить возможные дефекты.
– Этим летом мы завершили работы совместно с подрядной организацией, отправили сведения на экспертизу и получили в ответ интерпретацию этих значений, – рассказал Василий Суворов, заместитель начальника Медвежинского газопромыслового управления по производству. – Опираясь на результаты, мы определили точки, которые требуют дополнительного контроля. Сейчас на этих участках проходит очередной этап диагностики, уже своими силами.
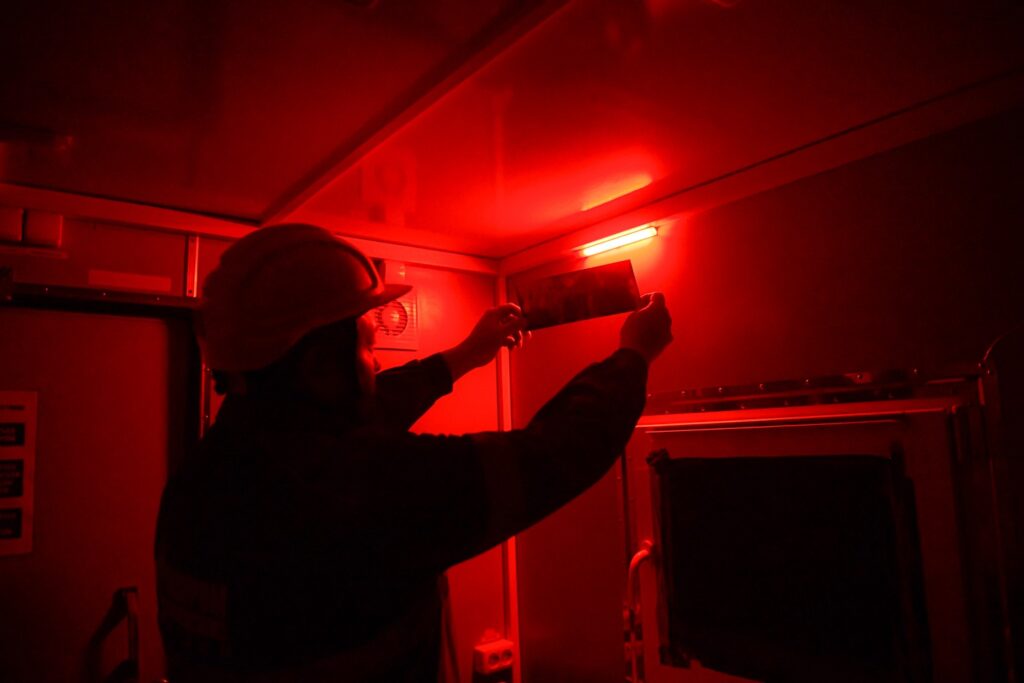
Каждый шаг просчитан наперёд, к задачам приступили параллельно на нескольких участках. Вовлечены буквально все филиалы компании. Пока на одной площадке выполняют отсыпку временной дороги, неподалёку заняты разработкой котлована, чтобы обеспечить доступ к трубопроводу. Ещё в нескольких километрах стоит полевая испытательная лаборатория. Скоро специалисты Инженерно-технического центра перейдут на точки, где сейчас для них готовят рабочее пространство. А пока завершают обследование на своей позиции. Они отвечают за самый ответственный элемент диагностической цепочки – радиографический контроль. Если по-простому – рентген для газопровода.

– На трубу накладываем плёнку, а с другой стороны устанавливаем устройство. При прохождении рентгеновских лучей через металл все возможные дефекты в теле трубы, детали стыка сварного шва отражаются на снимке, – объяснил Роман Щербов, дефектоскопист рентгено-, гаммаграфирования Инженерно-технического центра. – В зависимости от диаметра технологической нитки и толщины стенки используем рентгеновский аппарат подходящего типа – сейчас у нас с собой мощный, 250 киловатт. Отходим на безопасное по дозиметру расстояние и выполняем съёмку.
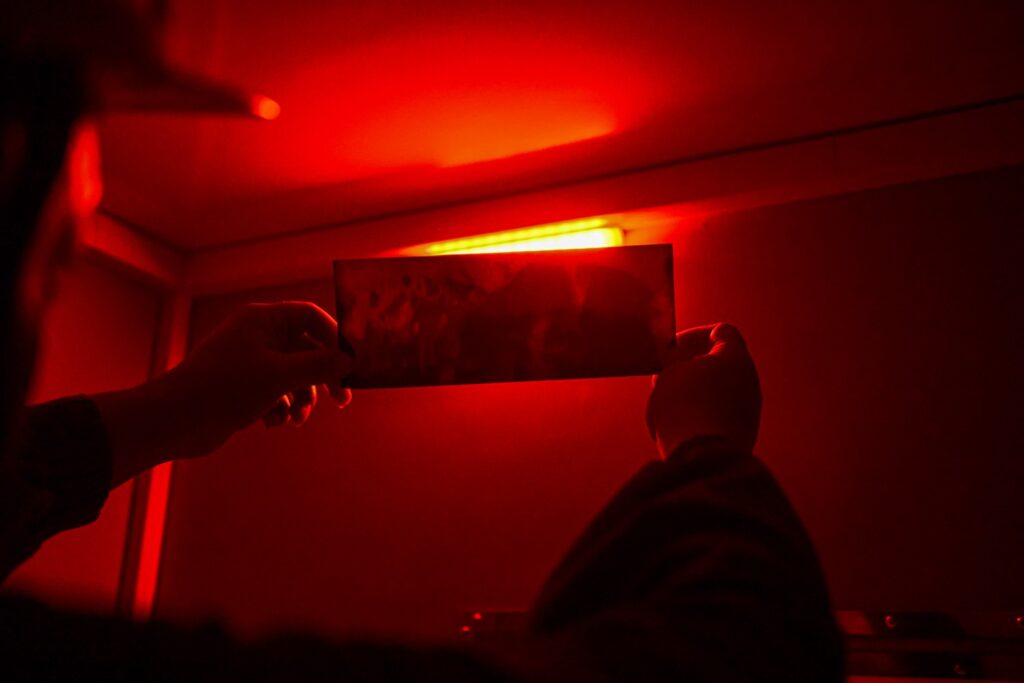
Проявляют плёнку здесь же, в полях. Под эту процедуру оборудована часть передвижной лаборатории. Красный свет, ванночки, фиксаторы – принцип тот же, что и с обычной фотоплёнкой. Затем каждый снимок в деталях рассматривают на негатоскопе – специальном приборе для расшифровки радиографических изображений.
Но и это ещё не всё. За рентгенографией следует ещё один контроль – ультразвуковой, дублирующий. Чтобы наверняка и окончательно убедиться в целостности стали. Метод снова напоминает знакомые нам исследования – оказалось, УЗИ проводят и трубопроводам. Никак иначе, если дело касается безопасности персонала и эксплуатируемых объектов. Для компании это новый, очередной формат профилактики.
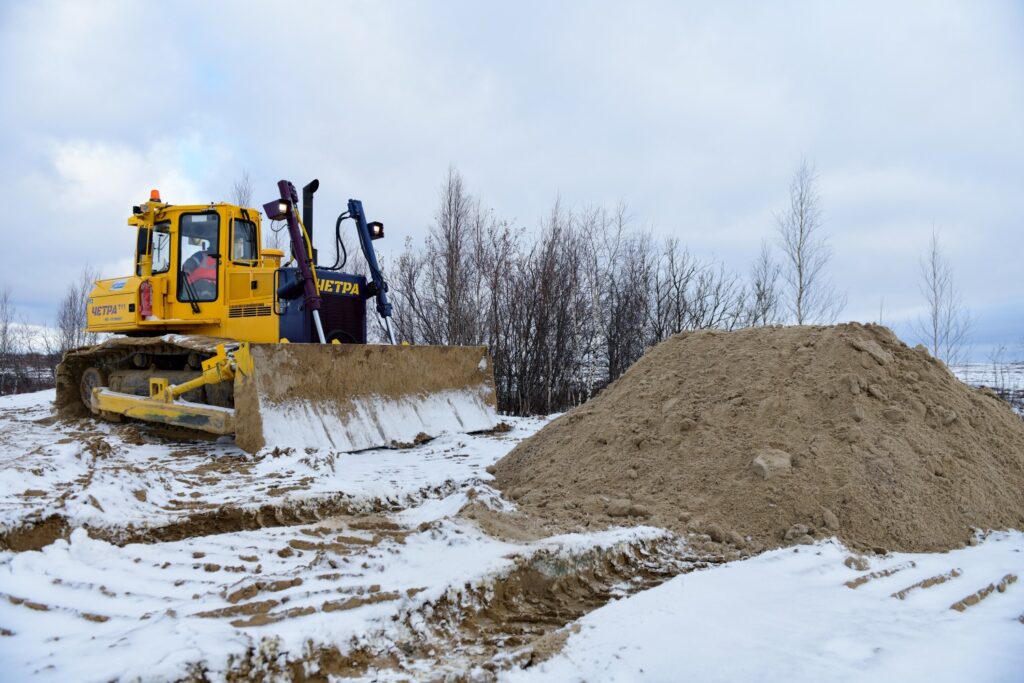
– В этом году внутритрубную диагностику провели впервые, полигоном для апробации технологии стал межпромысловый коллектор № 2 Медвежьего, а также газопровод подключения Ямсовейского промысла, – добавил Василий Суворов. – В перспективе комплекс работ будут проводить уже систематически.

После полевого этапа последует аналитический, с опорой на качественный массив данных. Так, методично, прогрессивно и основательно в коллективе заботятся об оборудовании на всех этапах добычи и подготовки газа.
Фото Игоря Букина